Industry Day 2022
Welcome to our Chair’s contribution to the ETH Zurich Industry Day 2022!
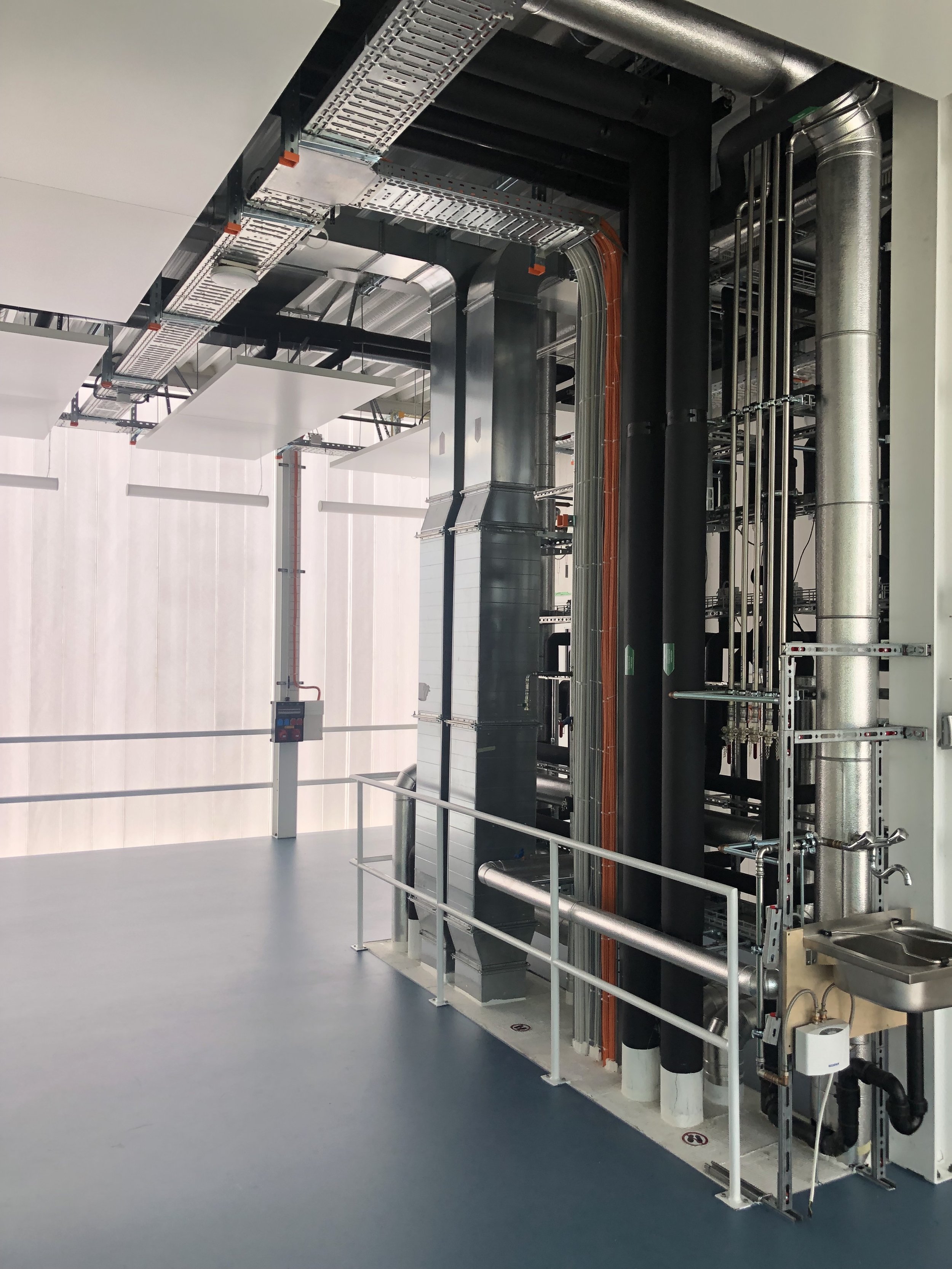
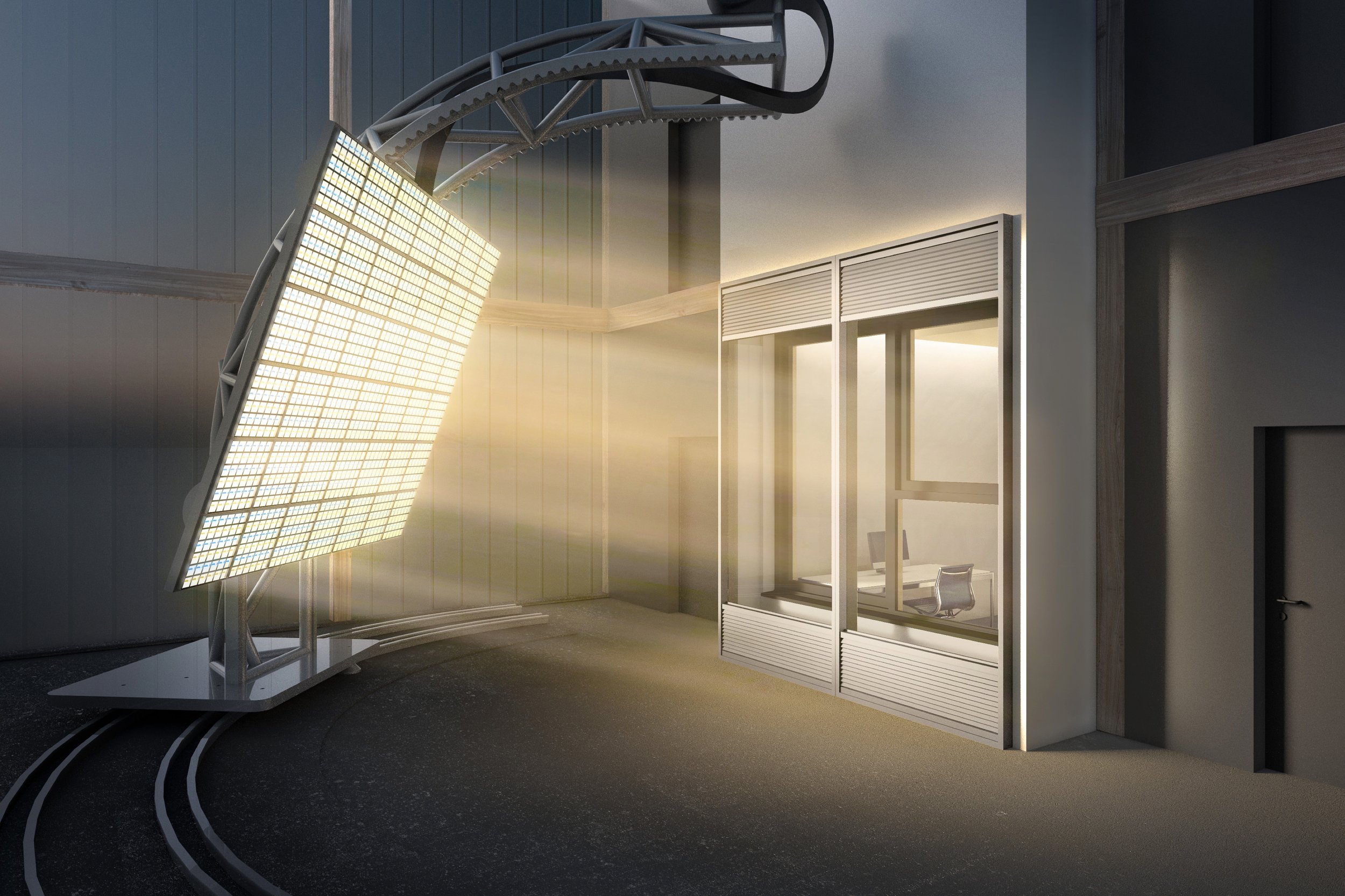
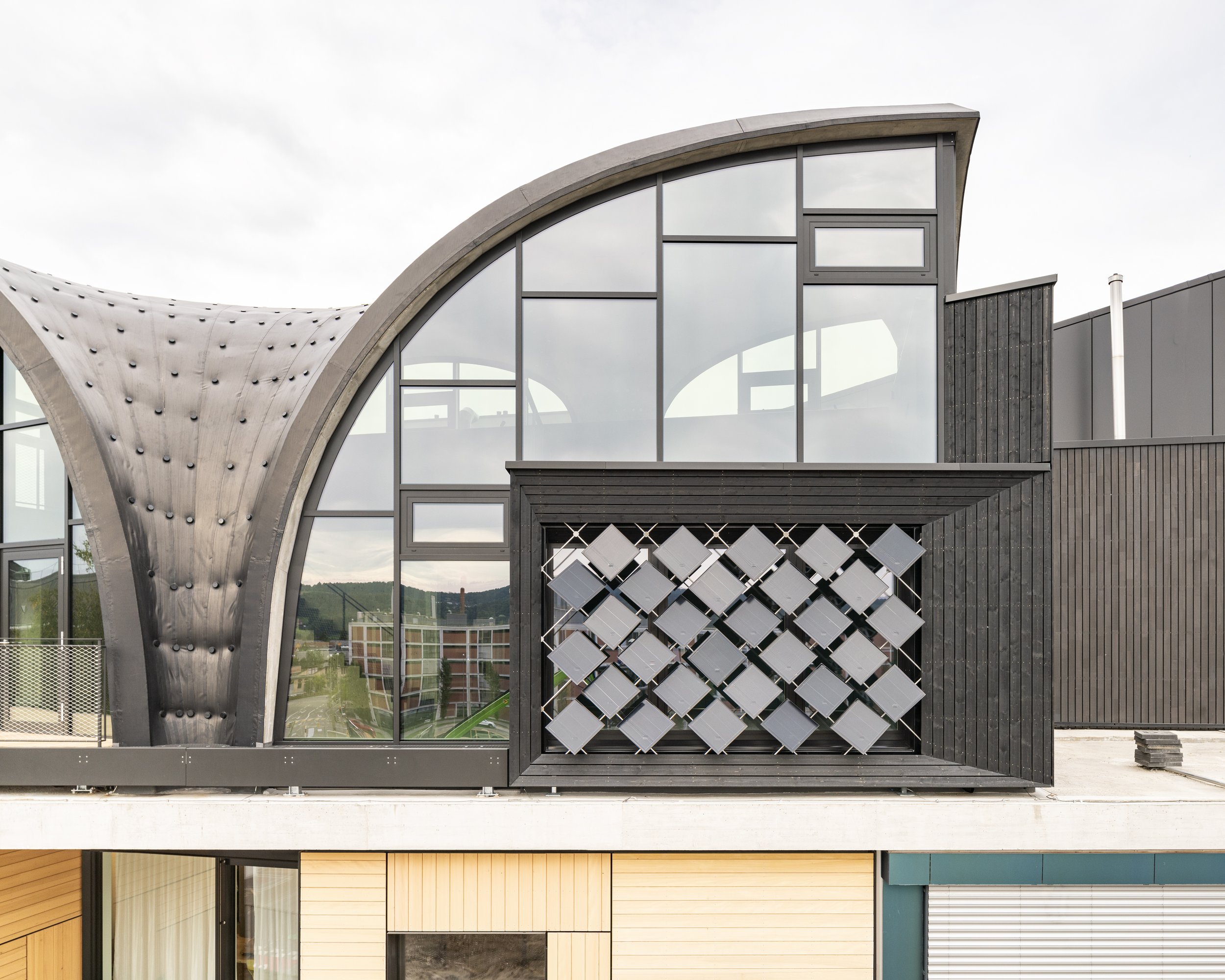
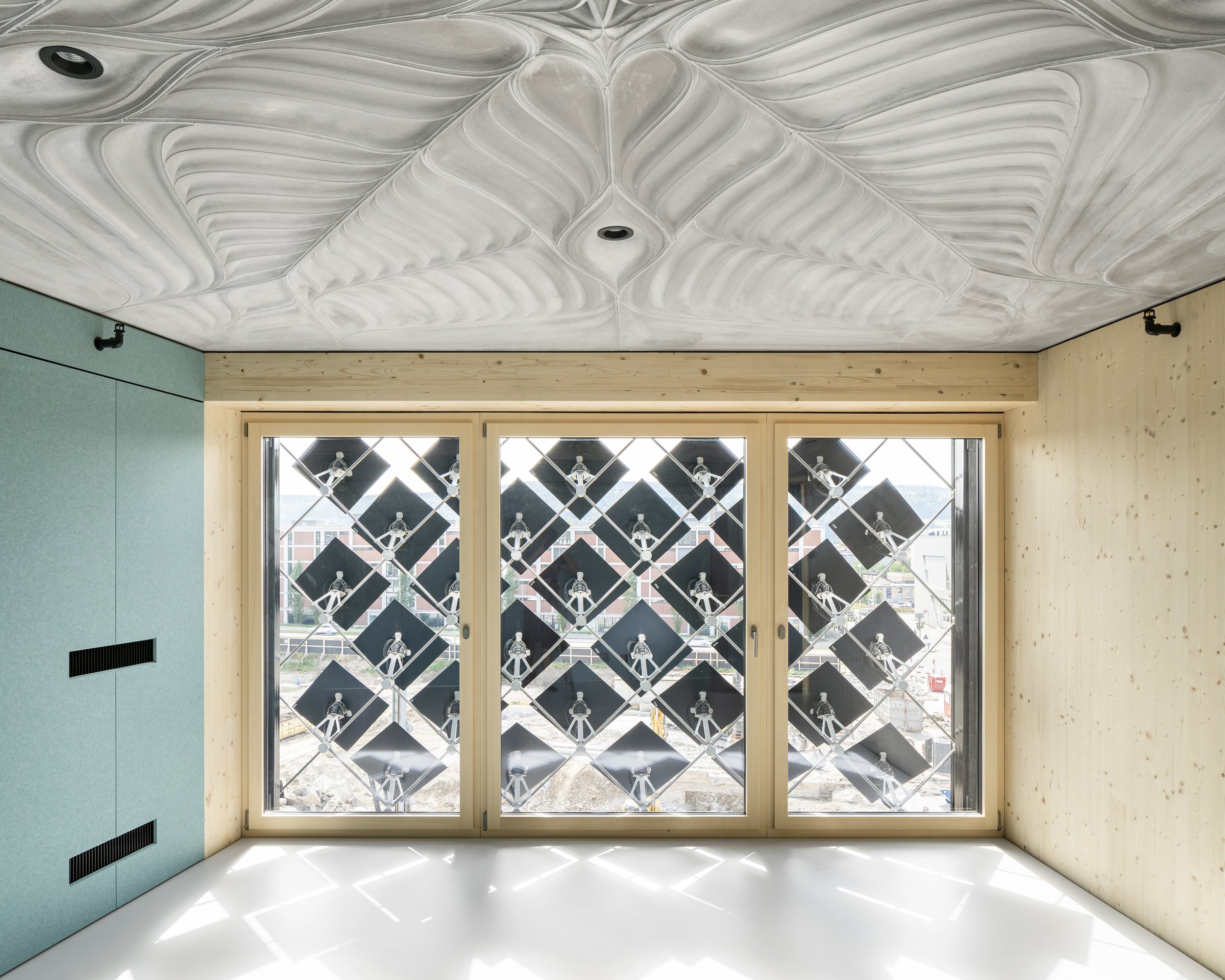
On this page, you will find additional information and links about our latest research topics.
About the new Zero Carbon Building Systems Lab
Initiated by the Chair of Architecture and Building Systems at ETH Zurich, the Zero Carbon Building Systems (ZCBS) Lab is a ground-breaking testing facility capable of conducting climatic experiments on a 1-to-1 building scale. The lab will support a wide range of research and testing of building technologies, as well as user acceptance and interaction studies. Specifically, research on building systems and components, from early proof-of-concept validation to system demonstration will be conducted at the lab.
The research at the Chair of Architecture and Buildings Systems focuses on efficient systems for zero energy, low emission and highly comfortable buildings.
The Zero Carbon Building Systems Lab (ZCBS) pioneers fundamental, experimental research linking the three essential building blocks of zero carbon building design: energy, materials and the human occupant.
Research at the lab addresses critical fields such as:
Next generation low carbon, multifunctional building components, e.g. envelopes, floors, walls, utilizing simulation and digital fabrication
Next generation integrated building systems for heating, cooling, energy generation and ventilation
Human-building interaction and bi-directional learning based on IoT Technology and Artificial Intelligence (AI)
The ZCBS lab offers a unique setting for collaborations between academia and industry, allowing to jointly develop testbed and validate innovative technological solutions before their application in the market.
Preview at the Industry Day 2022
During the Industry Day you have the opportunity to visit the ZCBS Lab, guided by our PhD researchers. Find the route and location on Google Maps: https://goo.gl/maps/bxNa6ipUPcwpGb9u8
Featured research
Bespoke Thermo-Optical Properties: Performance Integration in 3D Printed Building Facades
PhD Researcher: Valeria Piccioni
Concept for a 3DP facade. By understanding the interplay of material, fabrication and geometry we can design performant components integrating multiple requirements.
3D printing enables customised facades. Components with a tailored combination of optical, thermal and solar properties can be designed by tuning geometrical and fabrication parameters.
Large-scale polymer 3D printing. A custom extrusion set-up was developed by the NCCR team at the RFL enabling 1:1 facade components fabrication.
Multiscale research approach. Performance integration and assessment in 3DP facades requires modelling of the physical effects happening at the scale of material, component and building and information transfer between scales.
Tuning of optical properties through fabrication parameters. The extrusion process affects the material properties of polymers, thus the optical behaviour of 3D printed parts can be altered.
Layer morphology affects optical properties. The way plastic layers are deposited can be controlled to obtain angle-dependent transmission and light scattering properties.
3D printed facades with bespoke thermo-optical properties. In this study we show how fabrication parameters can be tuned to obtain facade components with angle-selective solar properties that ensure thermal and visual comfort.
3D printed cavity structures can achieve excellent thermal insulation. We study the thermal behaviour with experiments and simulation to retrieve design gudelines and performance indicators.
Prototype fabrication at multiple scales. The multiscale research approach encompasses printing of prototypes at small scale to inform 1:1 scale fabrication.
2. Moving Heat without Energy: 3D Printed Polymer Heat Pipes for Thermal Application
PhD Researcher: Bharath Seshadri
3D printing process of a vacuum tight Liquid Crystal Polymer heat pipe showing (a) FDM process and print path; polymer chain orientations within the filament (b) before and (c) after the heated extrusion, (d) cross section of the heat-pipe wall describing Layer Height (LH) and Layer Width (LW), (e) optical microscopic image of a the cross section wall (described in (d)) demonstrating the ‘core-shell’ morphology i.e. light colored shells and darker cores - indicating highly ordered shells and less-ordered cores, and (f) a description of vacuum induced surface pressure (∆P), and material- (QLM) and layer- (QLL) leakage through the walls of the heat-pipe, and (g) oriented polymer chains with high gas barrier properties.
(a-d) Polarized light microscopy of 3DP LCP samples cross-sections and side-views describe the interlayer adhesion resulting in differences in printing temperature (TN), layer height (LH,) and layer width to nozzle ratio (LW:DN). (e) Spiral and non-spiral tool-paths are demonstrated.
Gas barrier characterized by leakage rate (a) relative to TN at a constant LH = 0.1mm and (b)LH, at a constant TN = 3300C, and (c) relative to DN:LW and print-path (spiral and non-spiral) and annealing at optimal TN and LH; and (d) leakage testing conducted for longer than 800 hours for a 200mm 3D printed LCP cylinder fabricated using optimal TN, LH, LW:DN and spiral print-path.
Directions of heat-transfer relative to the layer orientation for a 3DP LCP heat-pipe; (b) thermal conductivity of 3DP heat-pipe wall of heat-transfer perpendicular to and along layers; (c) time-series profile of temperature along the surface (measured at 60, 120, and 180 mm) of a 3DP LCP hollow tube, and an evacuated and charged heat pipe; (d) computational fluid dynamics simulation of a multi-phase flow within the heat-pipe
(a) The geometry of a sample helical 3DP LCP heat-pipe, (b) computational fluid dynamics simulation of steam volume fraction within the heat-pipe, and (d) fluid temperature within the heat-pipe and (b) infra-red images of surface temperature.
3. Utilizing the Sun in the City: Multiscale Analysis of Integrated Photovolatics (BIPV / UIPV)
PhD Researcher: Justin McCarty
Reference BIPV projects viewable @ explorerise.com and contain summaries of key morphological criteria.
Output diagram of a scripting tool that builds BIPV arrays and allows for rapid, high-resolution simulation of buildings.
The proposed methodological workflow begins with the data collection process and works through a modeling procedure for a variety of UIPV simulation. Third, the simulated PV yield data will be analyzed through several lenses (LCOE, Carbon payback period, robustness, etc.). The results of the analysis will be used in an MCDA framework to rank the systems. The best-performing systems will be used to fill the projected capacity needs in an optimal urban energy district scenario or either case study.